Gofretni kesish texnologiyasi yarimo'tkazgichlarni ishlab chiqarish jarayonida muhim qadam sifatida chipning ishlashi, rentabelligi va ishlab chiqarish xarajatlari bilan bevosita bog'liq.
# 01 Gofretni kesishning foni va ahamiyati
1.1 Gofretni kesishning ta'rifi
Gofretlarni kesish (shuningdek, skriping deb ham ataladi) yarimo'tkazgich ishlab chiqarishdagi muhim qadam bo'lib, qayta ishlangan gofretlarni bir nechta individual qoliplarga bo'lishga qaratilgan. Ushbu qoliplar odatda elektron qurilmalarni ishlab chiqarishda ishlatiladigan asosiy komponentlar bo'lib, odatda to'liq elektron funksionallikni o'z ichiga oladi. Chip konstruksiyalari murakkablashib, o‘lchamlar qisqarishda davom etar ekan, gofretni kesish texnologiyasi uchun aniqlik va samaradorlik talablari tobora qattiqlashib bormoqda.
Amaliy operatsiyalarda gofretni kesish odatda har bir qolipning butunligi va to'liq ishlashini ta'minlash uchun olmos pichoqlari kabi yuqori aniqlikdagi asboblardan foydalanadi. Asosiy bosqichlarga kesishdan oldin tayyorgarlik, kesish jarayonida aniq nazorat va kesishdan keyin sifatni tekshirish kiradi.
Kesishdan oldin gofret aniq kesish yo'llarini ta'minlash uchun belgilanishi va joylashtirilishi kerak. Kesish jarayonida gofretning shikastlanishiga yo'l qo'ymaslik uchun asbob bosimi va tezligi kabi parametrlarni qat'iy nazorat qilish kerak. Kesishdan so'ng, har bir chip ishlash standartlariga javob berishini ta'minlash uchun keng qamrovli sifat tekshiruvlari o'tkaziladi.
Gofretni kesish texnologiyasining asosiy tamoyillari nafaqat kesish uskunasini tanlash va jarayon parametrlarini belgilashni, balki materiallarning mexanik xususiyatlari va xususiyatlarini kesish sifatiga ta'sirini ham o'z ichiga oladi. Misol uchun, past-k dielektrik kremniy gofretlari, past mexanik xususiyatlari tufayli, kesish paytida stress kontsentratsiyasiga juda sezgir bo'lib, parchalanish va yorilish kabi nosozliklarga olib keladi. Past qattiqlikdagi materiallarning past qattiqligi va mo'rtligi ularni mexanik kuch yoki termal stress ostida, ayniqsa kesish paytida strukturaviy shikastlanishga ko'proq moyil qiladi. Asbob va gofret yuzasi o'rtasidagi aloqa yuqori haroratlar bilan birgalikda stress kontsentratsiyasini yanada kuchaytirishi mumkin.
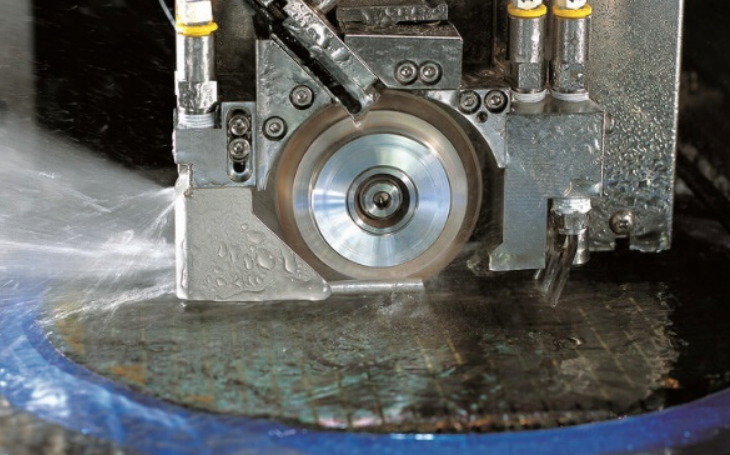
Materialshunoslik sohasidagi yutuqlar bilan gofretni kesish texnologiyasi an'anaviy kremniyga asoslangan yarimo'tkazgichlardan tashqari, galiy nitridi (GaN) kabi yangi materiallarni o'z ichiga oladi. Ushbu yangi materiallar, ularning qattiqligi va strukturaviy xususiyatlari tufayli, kesish jarayonlari uchun yangi muammolarni keltirib chiqaradi, bu esa kesish asboblari va texnikasini yanada takomillashtirishni talab qiladi.
Yarimo'tkazgich sanoatida muhim jarayon sifatida gofretni kesish rivojlanayotgan talablar va texnologik yutuqlarga javoban optimallashtirishda davom etmoqda va kelajakdagi mikroelektronika va integral mikrosxemalar texnologiyalari uchun zamin yaratadi.
Gofretlarni kesish texnologiyasini takomillashtirish yordamchi materiallar va asboblarni ishlab chiqishdan tashqarida. Ular, shuningdek, jarayonni optimallashtirish, uskunaning ishlashini yaxshilash va zar parametrlarini aniq nazorat qilishni o'z ichiga oladi. Ushbu yutuqlar gofretni kesish jarayonida yuqori aniqlik, samaradorlik va barqarorlikni ta'minlashga qaratilgan bo'lib, yarimo'tkazgich sanoatining kichikroq o'lchamlarga, yuqori integratsiyaga va yanada murakkab chip tuzilmalariga bo'lgan ehtiyojini qondiradi.
yaxshilash maydoni | Maxsus chora-tadbirlar | Effektlar |
Jarayonni optimallashtirish | - Dastlabki tayyorgarlikni yaxshilang, masalan, gofretni aniqroq joylashtirish va yo'lni rejalashtirish. | - Kesish xatolarini kamaytirish va barqarorlikni yaxshilash. |
- Kesish xatolarini minimallashtiring va barqarorlikni oshiring. | - Asbob bosimi, tezligi va haroratini sozlash uchun real vaqtda monitoring va qayta aloqa mexanizmlarini qabul qiling. | |
- Gofretning sinish tezligini pasaytiring va chip sifatini yaxshilang. | ||
Uskunalar unumdorligini oshirish | - Yuqori aniqlikdagi mexanik tizimlar va ilg'or avtomatlashtirishni boshqarish texnologiyasidan foydalaning. | - Kesish aniqligini oshiring va moddiy isrofni kamaytiring. |
- Yuqori qattiqlikdagi material gofretlari uchun mos lazerli kesish texnologiyasini joriy etish. | - Ishlab chiqarish samaradorligini oshirish va qo'lda xatolarni kamaytirish. | |
- Avtomatik monitoring va sozlash uchun uskunalarni avtomatlashtirishni oshirish. | ||
Parametrlarni aniq nazorat qilish | - Kesish chuqurligi, tezlik, asbob turi va sovutish usullari kabi parametrlarni nozik sozlang. | - Qolibning yaxlitligini va elektr ishlashini ta'minlash. |
- Gofret materiali, qalinligi va tuzilishi asosida parametrlarni moslashtiring. | - Hosildorlik darajasini oshirish, moddiy chiqindilarni kamaytirish va ishlab chiqarish xarajatlarini kamaytirish. | |
Strategik ahamiyati | - Doimiy ravishda yangi texnologik yo'llarni o'rganing, jarayonlarni optimallashtiring va bozor talablarini qondirish uchun uskunalar imkoniyatlarini oshiring. | - Chip ishlab chiqarish rentabelligi va ish faoliyatini yaxshilash, yangi materiallar va ilg'or chip dizaynlarini ishlab chiqishni qo'llab-quvvatlash. |
1.2 Gofretni kesishning ahamiyati
Gofretlarni kesish yarimo'tkazgichlarni ishlab chiqarish jarayonida muhim rol o'ynaydi, bu keyingi bosqichlarga, shuningdek, yakuniy mahsulot sifati va ishlashiga bevosita ta'sir qiladi. Uning ahamiyatini quyidagicha batafsil bayon qilish mumkin:
Birinchidan, kesishning aniqligi va izchilligi chip hosildorligi va ishonchliligini ta'minlash uchun kalit hisoblanadi. Ishlab chiqarish jarayonida gofretlar ko'plab murakkab sxema tuzilmalarini hosil qilish uchun bir nechta ishlov berish bosqichlaridan o'tadi, ular alohida chiplarga (matritsalarga) bo'linishi kerak. Agar kesish jarayonida tekislash yoki kesishda jiddiy xatolar bo'lsa, sxemalar shikastlanishi mumkin, bu chipning funksionalligi va ishonchliligiga ta'sir qiladi. Shu sababli, yuqori aniqlikdagi dising texnologiyasi nafaqat har bir chipning yaxlitligini ta'minlabgina qolmay, balki ichki kontaktlarning zanglashiga olib kelishiga yo'l qo'ymaydi, umumiy rentabellikni yaxshilaydi.
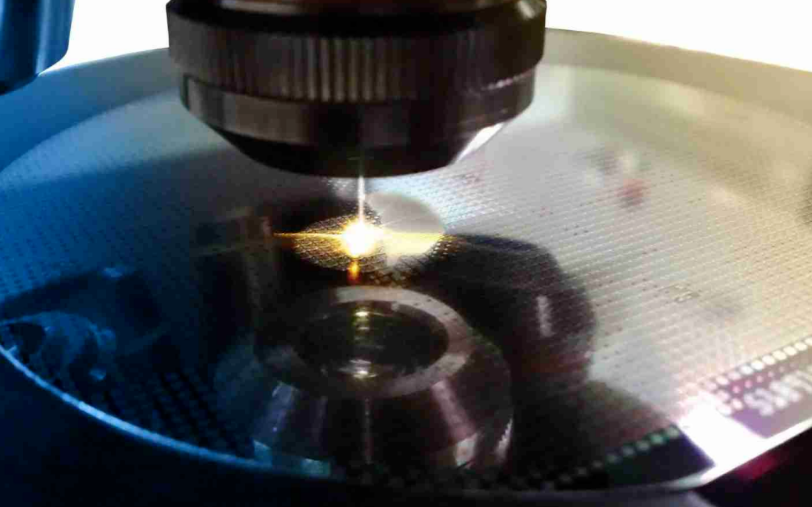
Ikkinchidan, gofretni kesish ishlab chiqarish samaradorligi va xarajatlarni nazorat qilishga sezilarli ta'sir ko'rsatadi. Ishlab chiqarish jarayonidagi hal qiluvchi bosqich sifatida uning samaradorligi keyingi bosqichlarning borishiga bevosita ta'sir qiladi. Kesish jarayonini optimallashtirish, avtomatlashtirish darajasini oshirish va kesish tezligini yaxshilash orqali umumiy ishlab chiqarish samaradorligini sezilarli darajada oshirish mumkin.
Boshqa tomondan, kesish paytida materialning isrof qilinishi xarajatlarni boshqarishda hal qiluvchi omil hisoblanadi. Ilg'or kublarni kesish texnologiyalaridan foydalanish nafaqat kesish jarayonida keraksiz moddiy yo'qotishlarni kamaytiradi, balki gofretdan foydalanishni oshiradi va shu bilan ishlab chiqarish xarajatlarini kamaytiradi.
Yarimo'tkazgich texnologiyasidagi yutuqlar bilan gofret diametrlari o'sishda davom etmoqda va kontaktlarning zanglashiga olib keladigan zichligi shunga mos ravishda oshib boradi, bu esa kublarni kesish texnologiyasiga yuqori talablarni qo'yadi. Kattaroq gofretlar kesish yo'llarini aniqroq nazorat qilishni talab qiladi, ayniqsa yuqori zichlikdagi kontaktlarning zanglashiga olib keladigan joylarida, hatto kichik og'ishlar ham bir nechta chiplarni nuqsonli holga keltirishi mumkin. Bundan tashqari, kattaroq gofretlar ko'proq kesish chiziqlari va murakkabroq jarayon bosqichlarini o'z ichiga oladi, bu esa ushbu qiyinchiliklarga javob berish uchun kublarni kesish texnologiyalarining aniqligi, mustahkamligi va samaradorligini yanada yaxshilashni talab qiladi.
1.3 Gofretni kesish jarayoni
Gofretni kesish jarayoni tayyorgarlik bosqichidan yakuniy sifat nazoratigacha bo'lgan barcha bosqichlarni o'z ichiga oladi, har bir bosqich kesilgan chiplarning sifati va ishlashini ta'minlash uchun juda muhimdir. Quyida har bir bosqichning batafsil tavsifi keltirilgan.
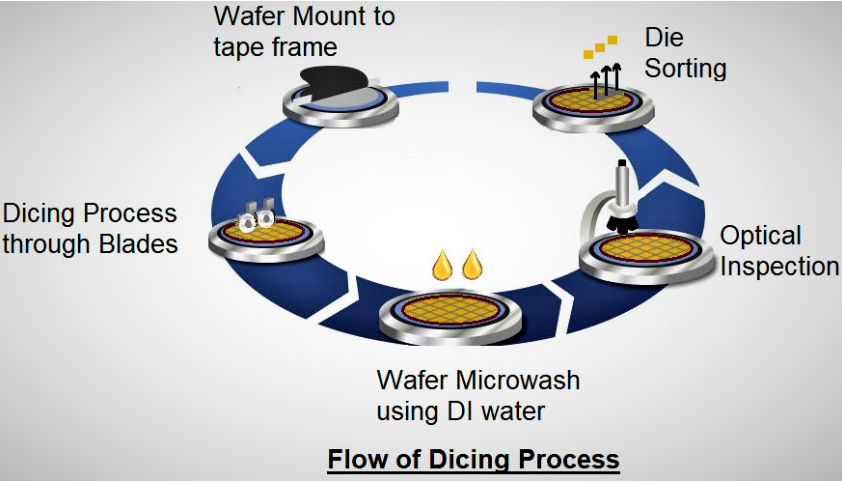
Bosqich | Batafsil tavsif |
Tayyorgarlik bosqichi | -Gofretni tozalash: Nopokliklar, zarralar va ifloslantiruvchi moddalarni olib tashlash, toza sirtni ta'minlash uchun ultratovush yoki mexanik tozalash bilan birgalikda yuqori toza suv va maxsus tozalash vositalaridan foydalaning. -Aniq joylashishni aniqlash: Gofret mo'ljallangan kesish yo'llari bo'ylab to'g'ri taqsimlanishini ta'minlash uchun yuqori aniqlikdagi uskunadan foydalaning. -Gofretni mahkamlash: Tebranish yoki harakatdan shikastlanmaslik uchun kesish vaqtida barqarorlikni saqlash uchun gofretni lenta ramkasiga mahkamlang. |
Kesish bosqichi | -Pichoqni kesish: Jismoniy kesish uchun yuqori tezlikda aylanadigan olmos bilan qoplangan pichoqlarni ishlating, kremniy asosidagi materiallarga mos keladi va tejamkor. -Lazer bilan kesish: Kontaktsiz kesish uchun yuqori energiyali lazer nurlaridan foydalaning, galliy nitridi kabi mo'rt yoki yuqori qattiqlikdagi materiallar uchun ideal, yuqori aniqlik va kamroq material yo'qotilishini ta'minlaydi. -Yangi texnologiyalar: Issiqlikdan ta'sirlangan zonalarni minimallashtirishda samaradorlik va aniqlikni yanada oshirish uchun lazer va plazma kesish texnologiyalarini joriy etish. |
Tozalash bosqichi | - Kesish paytida hosil bo'lgan qoldiqlar va changlarni keyingi jarayonlarga yoki chipning elektr ishlashiga ta'sir qilishiga yo'l qo'ymaslik uchun ultratovush yoki buzadigan amallar bilan tozalash bilan birgalikda deionizatsiyalangan suv (DI suv) va maxsus tozalash vositalaridan foydalaning. - Yuqori tozalikdagi DI suvi yangi ifloslantiruvchi moddalarni kiritishdan qochadi va toza gofret muhitini ta'minlaydi. |
Tekshirish bosqichi | -Optik tekshirish: Qusurlarni tezda aniqlash, maydalangan chiplarda yoriqlar yoki chiplar boʻlmasligini taʼminlash, tekshirish samaradorligini oshirish va inson xatosini kamaytirish uchun sunʼiy intellekt algoritmlari bilan birgalikda optik aniqlash tizimlaridan foydalaning. -O'lchov o'lchovi: Chip o'lchamlari dizayn xususiyatlariga mos kelishini tekshiring. -Elektr ishlashi testi: Muhim chiplarning elektr ishlashi standartlarga javob berishini ta'minlash, keyingi ilovalarda ishonchlilikni kafolatlash. |
Saralash bosqichi | - Tasma ramkasidan malakali chiplarni ajratish uchun robot qo'llari yoki vakuumli so'rg'ichlardan foydalaning va ularni ishlashga qarab avtomatik ravishda saralang, bu esa aniqlikni oshirish bilan birga ishlab chiqarish samaradorligi va moslashuvchanligini ta'minlaydi. |
Gofretni kesish jarayoni gofretni tozalash, joylashtirish, kesish, tozalash, tekshirish va saralashni o'z ichiga oladi, har bir qadam juda muhim. Avtomatlashtirish, lazerli kesish va sun'iy intellektni tekshirish texnologiyalaridagi yutuqlar bilan zamonaviy gofretni kesish tizimlari yuqori aniqlik, tezlik va materiallar yo'qotilishini kamaytirishi mumkin. Kelajakda lazer va plazma kabi yangi kesish texnologiyalari asta-sekin an'anaviy pichoqni kesish o'rnini bosadi, bu esa yarimo'tkazgichlarni ishlab chiqarish jarayonlarining rivojlanishini yanada kuchaytiradi.
Gofretni kesish texnologiyasi va uning tamoyillari
Rasmda gofretni kesishning uchta umumiy texnologiyasi tasvirlangan:Pichoqni kesish,Lazer bilan kesish, vaPlazma bo'laklari. Quyida ushbu uchta texnikaning batafsil tahlili va qo'shimcha tushuntirishlari keltirilgan:
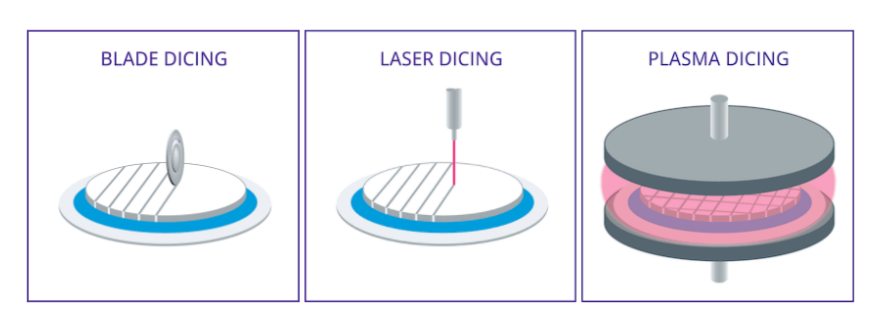
Yarimo'tkazgich ishlab chiqarishda gofretni kesish juda muhim bosqich bo'lib, gofret qalinligidan kelib chiqqan holda tegishli kesish usulini tanlashni talab qiladi. Birinchi qadam gofretning qalinligini aniqlashdir. Gofret qalinligi 100 mikrondan oshsa, pichoqni kesish usuli kesish usuli sifatida tanlanishi mumkin. Agar pichoqni kesish mos bo'lmasa, singan bo'laklarni kesish usuli qo'llanilishi mumkin, bu ham yozuvchi kesish, ham pichoqni kesish usullarini o'z ichiga oladi.
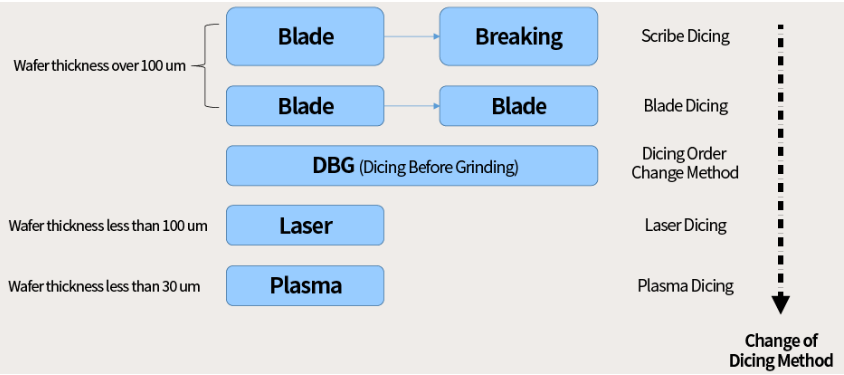
Gofret qalinligi 30 dan 100 mikrongacha bo'lganida, DBG (Dice Before Grinding) usuli tavsiya etiladi. Bunday holda, eng yaxshi natijalarga erishish uchun kerak bo'lganda skriptni kesish, pichoqni kesish yoki kesish ketma-ketligini sozlash tanlanishi mumkin.
Qalinligi 30 mikrondan kam bo'lgan o'ta yupqa gofretlar uchun lazer bilan kesish uning nozik gofretlarni haddan tashqari shikastlanmasdan aniq kesish qobiliyati tufayli afzal qilingan usulga aylanadi. Agar lazerni kesish muayyan talablarga javob bermasa, plazma bilan kesish alternativa sifatida ishlatilishi mumkin. Ushbu oqim sxemasi turli xil qalinlik sharoitida eng mos gofretni kesish texnologiyasini tanlashni ta'minlash uchun aniq qaror qabul qilish yo'lini taqdim etadi.
2.1 Mexanik kesish texnologiyasi
Mexanik kesish texnologiyasi gofretni kesishning an'anaviy usuli hisoblanadi. Asosiy printsip gofretni kesish uchun kesish vositasi sifatida yuqori tezlikda aylanadigan olmosli silliqlash g'ildiragidan foydalanishdir. Asosiy jihozlar oldindan belgilangan kesish yo'li bo'ylab aniq kesish yoki yiv ochish uchun olmosli silliqlash g'ildiragi asbobini yuqori tezlikda boshqaradigan havo rulmanli milni o'z ichiga oladi. Ushbu texnologiya arzonligi, yuqori samaradorligi va keng qo'llanilishi tufayli sanoatda keng qo'llaniladi.
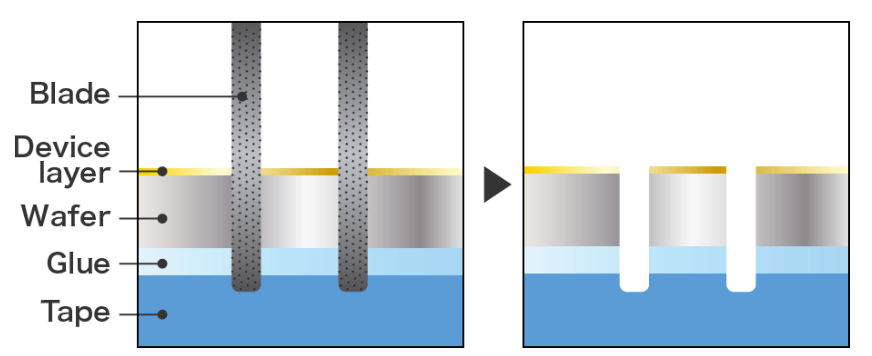
Afzalliklar
Olmosli silliqlash g'ildiragi asboblarining yuqori qattiqligi va aşınma qarshiligi mexanik kesish texnologiyasini an'anaviy kremniyga asoslangan materiallar yoki yangi aralash yarimo'tkazgichlar bo'ladimi, turli xil gofret materiallarini kesish ehtiyojlariga moslashishga imkon beradi. Uning ishlashi oddiy, nisbatan past texnik talablarga ega bo'lib, ommaviy ishlab chiqarishda mashhurligini yanada oshiradi. Bundan tashqari, lazerni kesish kabi boshqa kesish usullari bilan solishtirganda, mexanik kesish ko'proq nazorat qilinadigan xarajatlarga ega bo'lib, uni yuqori hajmli ishlab chiqarish ehtiyojlariga moslashtiradi.
Cheklovlar
Ko'p afzalliklariga qaramay, mexanik kesish texnologiyasi ham cheklovlarga ega. Birinchidan, asbob va gofret o'rtasidagi jismoniy aloqa tufayli, kesish aniqligi nisbatan cheklangan bo'lib, ko'pincha keyingi chiplarni qadoqlash va sinovdan o'tkazishning aniqligiga ta'sir qilishi mumkin bo'lgan o'lchovli og'ishlarga olib keladi. Ikkinchidan, mexanik kesish jarayonida parchalanish va yoriqlar kabi nuqsonlar osongina paydo bo'lishi mumkin, bu nafaqat hosildorlikka ta'sir qiladi, balki chiplarning ishonchliligi va ishlash muddatiga ham salbiy ta'sir ko'rsatishi mumkin. Mexanik stressdan kelib chiqadigan shikastlanish, ayniqsa, yuqori zichlikdagi chiplarni ishlab chiqarish uchun, ayniqsa, bu muammolar ko'proq bo'lgan mo'rt materiallarni kesishda zararli.
Texnologik takomillashtirish
Ushbu cheklovlarni bartaraf etish uchun tadqiqotchilar mexanik kesish jarayonini doimiy ravishda optimallashtiradilar. Asosiy yaxshilanishlar kesish aniqligi va chidamliligini oshirish uchun silliqlash g'ildiraklarining dizayni va material tanlashini yaxshilashni o'z ichiga oladi. Bundan tashqari, kesish uskunasining konstruktiv dizayni va boshqaruv tizimlarini optimallashtirish kesish jarayonining barqarorligi va avtomatizatsiyasini yanada yaxshiladi. Ushbu yutuqlar inson harakatlaridan kelib chiqadigan xatolarni kamaytiradi va kesishlarning mustahkamligini yaxshilaydi. Kesish jarayonida anomaliyalarni real vaqt rejimida kuzatish uchun ilg‘or inspeksiya va sifat nazorati texnologiyalarining joriy etilishi ham kesish ishonchliligi va hosildorligini sezilarli darajada oshirdi.
Kelajakdagi taraqqiyot va yangi texnologiyalar
Mexanik kesish texnologiyasi hali ham gofretni kesishda muhim mavqega ega bo'lsa-da, yarimo'tkazgich jarayonlari rivojlanishi bilan yangi kesish texnologiyalari jadal rivojlanmoqda. Masalan, termal lazerni kesish texnologiyasini qo'llash mexanik kesishda aniqlik va nuqsonlar muammolariga yangi echimlarni beradi. Ushbu kontaktsiz kesish usuli gofretdagi jismoniy stressni kamaytiradi, ayniqsa, ko'proq mo'rt materiallarni kesishda parchalanish va yorilish holatlarini sezilarli darajada kamaytiradi. Kelajakda mexanik kesish texnologiyasini paydo bo'lgan kesish texnikasi bilan integratsiyalashuvi yarimo'tkazgich ishlab chiqarishni ko'proq imkoniyatlar va moslashuvchanlik bilan ta'minlaydi, ishlab chiqarish samaradorligi va chip sifatini yanada oshiradi.
Xulosa qilib aytish mumkinki, mexanik kesish texnologiyasi ma'lum kamchiliklarga ega bo'lsa-da, doimiy texnologik takomillashtirish va uning yangi kesish texnikasi bilan integratsiyalashuvi yarimo'tkazgichlarni ishlab chiqarishda hali ham muhim rol o'ynashga va kelajakdagi jarayonlarda raqobatbardoshligini saqlab qolishga imkon beradi.
2.2 Lazer bilan kesish texnologiyasi
Lazerni kesish texnologiyasi, gofretni kesishda yangi usul sifatida, yuqori aniqlik, mexanik aloqa shikastlanishining yo'qligi va tez kesish qobiliyati tufayli yarimo'tkazgich sanoatida asta-sekin keng e'tiborga sazovor bo'ldi. Ushbu texnologiya lazer nurlarining yuqori energiya zichligi va fokuslash qobiliyatidan gofret materiali yuzasida kichik issiqlik ta'sir qiladigan zonani yaratish uchun foydalanadi. Lazer nurlari gofretga qo'llanilganda, hosil bo'lgan termal kuchlanish materialning belgilangan joyda sinishiga olib keladi va aniq kesishga erishadi.
Lazerli kesish texnologiyasining afzalliklari
• Yuqori aniqlik: Lazer nurlarining aniq joylashishni aniqlash qobiliyati zamonaviy yuqori aniqlikdagi, yuqori zichlikdagi integral mikrosxemalar ishlab chiqarish talablariga javob beruvchi mikron yoki hatto nanometr darajasida kesish aniqligiga imkon beradi.
• Mexanik aloqa yo'q: Lazer bilan kesish gofret bilan jismoniy aloqa qilishdan qochadi, mexanik kesishda maydalash va yorilish kabi keng tarqalgan muammolarni oldini oladi, chiplarning rentabelligi va ishonchliligini sezilarli darajada yaxshilaydi.
• Tez kesish tezligi: Lazerli kesishning yuqori tezligi ishlab chiqarish samaradorligini oshirishga yordam beradi, bu uni keng ko'lamli, yuqori tezlikda ishlab chiqarish stsenariylari uchun ayniqsa mos keladi.
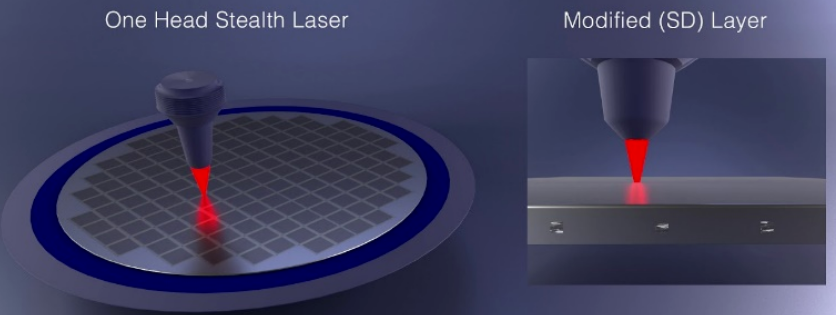
Qiyinchiliklar
• Uskunaning yuqori narxi: Lazerli kesish uskunalari uchun dastlabki sarmoyalar yuqori, bu ayniqsa kichik va o'rta ishlab chiqarish korxonalari uchun iqtisodiy bosimni keltirib chiqaradi.
• Jarayonni kompleks boshqarish: Lazer bilan kesish bir necha parametrlarni, jumladan energiya zichligi, fokus holati va kesish tezligini aniq nazorat qilishni talab qiladi, bu jarayonni murakkablashtiradi.
• Issiqlikdan ta'sirlangan zona muammolari: Lazerli kesishning kontaktsiz tabiati mexanik shikastlanishni kamaytiradigan bo'lsa-da, issiqlik ta'sir qiladigan zona (HAZ) tufayli yuzaga keladigan termal stress gofret materialining xususiyatlariga salbiy ta'sir ko'rsatishi mumkin. Ushbu ta'sirni minimallashtirish uchun jarayonni yanada optimallashtirish kerak.
Texnologik takomillashtirish yo'nalishlari
Ushbu muammolarni hal qilish uchun tadqiqotchilar uskunalar narxini pasaytirish, kesish samaradorligini oshirish va jarayon oqimini optimallashtirishga e'tibor qaratmoqda.
• Samarali lazerlar va optik tizimlar: Samaradorroq lazerlar va ilg'or optik tizimlarni ishlab chiqish orqali kesish aniqligi va tezligini oshirish bilan birga asbob-uskuna xarajatlarini kamaytirish mumkin.
• Jarayon parametrlarini optimallashtirish: Issiqlik ta'sir qiladigan zonani kamaytiradigan jarayonlarni takomillashtirish va shu bilan kesish sifatini yaxshilash uchun lazerlar va gofret materiallari o'rtasidagi o'zaro ta'sir bo'yicha chuqur tadqiqotlar olib borilmoqda.
• Intellektual boshqaruv tizimlari: Intellektual boshqaruv texnologiyalarini ishlab chiqish lazerni kesish jarayonini avtomatlashtirish va optimallashtirish, uning barqarorligi va izchilligini yaxshilashga qaratilgan.
Lazerli kesish texnologiyasi, ayniqsa, ultra yupqa gofretlar va yuqori aniqlikdagi kesish stsenariylarida samarali. Gofret o'lchamlari ortib borishi va kontaktlarning zanglashiga olib keladigan zichligi oshishi bilan an'anaviy mexanik kesish usullari zamonaviy yarimo'tkazgichlar ishlab chiqarishning yuqori aniqlik va yuqori samarali talablarini qondirish uchun kurashadi. Noyob afzalliklari tufayli lazerni kesish ushbu sohalarda afzal qilingan echimga aylanmoqda.
Lazerni kesish texnologiyasi hali ham yuqori uskunalar narxi va jarayonning murakkabligi kabi qiyinchiliklarga duch kelsa-da, uning yuqori aniqlikdagi va kontaktsiz shikastlanishdagi noyob afzalliklari uni yarimo'tkazgichlar ishlab chiqarishda rivojlanishning muhim yo'nalishiga aylantiradi. Lazer texnologiyasi va aqlli boshqaruv tizimlari rivojlanishda davom etar ekan, lazerni kesish gofretni kesish samaradorligi va sifatini yanada yaxshilashi kutilmoqda, bu esa yarimo'tkazgich sanoatining uzluksiz rivojlanishini ta'minlaydi.
2.3 Plazma bilan kesish texnologiyasi
Plazma kesish texnologiyasi, yangi paydo bo'lgan gofretni kesish usuli sifatida, so'nggi yillarda katta e'tibor qozondi. Ushbu texnologiya plazma nurlarining energiyasini, tezligini va kesish yo'lini nazorat qilish orqali gofretlarni aniq kesish uchun yuqori energiyali plazma nurlaridan foydalanadi va optimal kesish natijalariga erishadi.
Ishlash printsipi va afzalliklari
Plazma kesish jarayoni uskuna tomonidan ishlab chiqarilgan yuqori haroratli, yuqori energiyali plazma nuriga tayanadi. Ushbu nur gofret materialini juda qisqa vaqt ichida erish yoki bug'lanish nuqtasiga qizdirib, tez kesish imkonini beradi. An'anaviy mexanik yoki lazerli kesish bilan solishtirganda, plazma bilan kesish tezroq va kichikroq issiqlik ta'sir qiladigan zonani hosil qiladi, kesish paytida yoriqlar va shikastlanishlar paydo bo'lishini samarali ravishda kamaytiradi.
Amaliy ilovalarda plazma kesish texnologiyasi, ayniqsa, murakkab shakldagi gofretlarni qayta ishlashda mohirdir. Uning yuqori energiyali, sozlanishi plazma nuri tartibsiz shakldagi gofretlarni yuqori aniqlik bilan osongina kesishi mumkin. Shu sababli, mikroelektronika ishlab chiqarishda, ayniqsa, yuqori darajadagi chiplarni moslashtirilgan va kichik partiyalar ishlab chiqarishda ushbu texnologiya keng tarqalgan foydalanish uchun katta va'da beradi.
Qiyinchiliklar va cheklovlar
Plazma kesish texnologiyasining ko'plab afzalliklariga qaramasdan, u ham ba'zi qiyinchiliklarga duch keladi.
• Murakkab jarayon: Plazma kesish jarayoni murakkab va ta'minlash uchun yuqori aniqlikdagi uskunalar va tajribali operatorlar talab qilinadikesishda aniqlik va barqarorlik.
• Ekologik nazorat va xavfsizlik: Plazma nurining yuqori haroratli, yuqori energiyali tabiati qattiq ekologik nazorat va xavfsizlik choralarini talab qiladi, bu esa amalga oshirishning murakkabligi va narxini oshiradi.
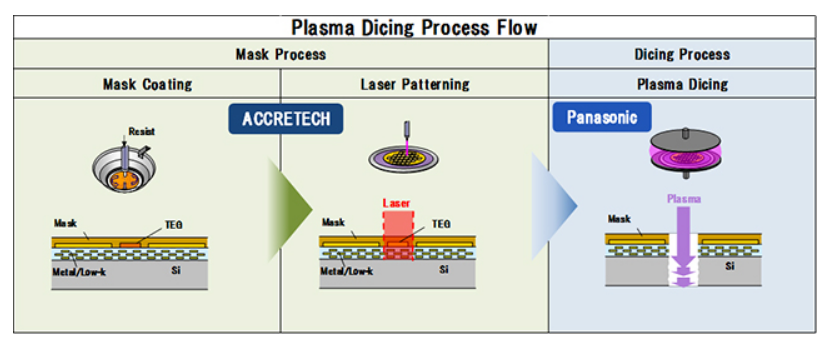
Kelajakdagi rivojlanish yo'nalishlari
Texnologik taraqqiyot bilan plazma bilan kesish bilan bog'liq qiyinchiliklar asta-sekin yengib chiqilishi kutilmoqda. Aqlliroq va barqaror kesish uskunalarini ishlab chiqish orqali qo'lda operatsiyalarga bog'liqlikni kamaytirish mumkin, bu esa ishlab chiqarish samaradorligini oshiradi. Shu bilan birga, jarayon parametrlarini va kesish muhitini optimallashtirish xavfsizlik xatarlari va operatsion xarajatlarni kamaytirishga yordam beradi.
Yarimo'tkazgichlar sanoatida gofretni kesish va kublarni kesish texnologiyasidagi innovatsiyalar sanoatni rivojlantirish uchun juda muhimdir. Plazma kesish texnologiyasi o'zining yuqori aniqligi, samaradorligi va murakkab gofret shakllarini boshqarish qobiliyati bilan ushbu sohada muhim yangi o'yinchi sifatida paydo bo'ldi. Ba'zi muammolar saqlanib qolayotgan bo'lsa-da, bu masalalar asta-sekin texnologik innovatsiyalar bilan hal qilinadi va yarimo'tkazgichlar ishlab chiqarishga ko'proq imkoniyatlar va imkoniyatlarni olib keladi.
Plazma kesish texnologiyasini qo'llash istiqbollari juda katta va kelajakda yarimo'tkazgichlarni ishlab chiqarishda muhim rol o'ynashi kutilmoqda. Uzluksiz texnologik innovatsiyalar va optimallashtirish orqali plazma bilan kesish nafaqat mavjud muammolarni hal qiladi, balki yarimo'tkazgich sanoati rivojlanishining kuchli haydovchisiga aylanadi.
2.4 Chiqib ketish sifati va ta'sir etuvchi omillar
Gofretni kesish sifati keyingi chiplarni qadoqlash, sinovdan o'tkazish va yakuniy mahsulotning umumiy ishlashi va ishonchliligi uchun juda muhimdir. Kesish paytida uchraydigan umumiy muammolar orasida yoriqlar, chiplar va kesish og'ishlari mavjud. Ushbu muammolarga birgalikda ishlaydigan bir nechta omillar ta'sir qiladi.
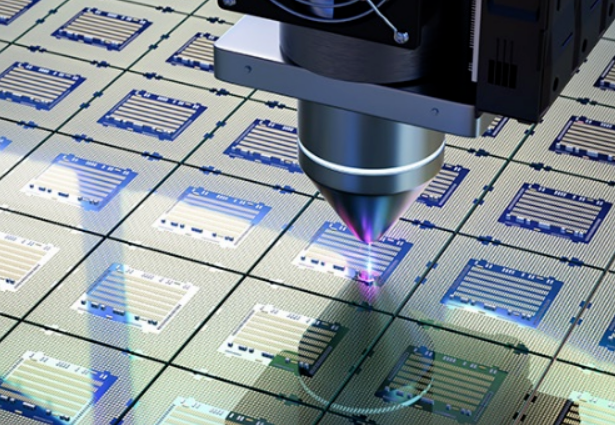
Turkum | Tarkib | Ta'sir |
Jarayon parametrlari | Kesish tezligi, besleme tezligi va kesish chuqurligi kesish jarayonining barqarorligi va aniqligiga bevosita ta'sir qiladi. Noto'g'ri sozlamalar stress kontsentratsiyasiga va haddan tashqari issiqlik ta'sir zonasiga olib kelishi mumkin, natijada yoriqlar va chiplar paydo bo'ladi. Parametrlarni gofret materiali, qalinligi va kesish talablariga muvofiq mos ravishda sozlash kerakli kesish natijalariga erishish uchun kalit hisoblanadi. | To'g'ri jarayon parametrlari aniq kesishni ta'minlaydi va yoriqlar va chiplar kabi nuqsonlar xavfini kamaytiradi. |
Uskunalar va moddiy omillar | -Pichoq sifati: Pichoqning materiali, qattiqligi va aşınma qarshiligi kesish jarayonining silliqligiga va kesilgan yuzaning tekisligiga ta'sir qiladi. Sifatsiz pichoqlar ishqalanish va termal kuchlanishni oshiradi, bu esa yoriqlar yoki parchalanishga olib keladi. To'g'ri pichoq materialini tanlash juda muhimdir. -Sovutish suyuqligining ishlashi: Sovutgichlar kesish haroratini kamaytirishga, ishqalanishni kamaytirishga va qoldiqlarni tozalashga yordam beradi. Samarasiz sovutish suvi yuqori harorat va qoldiqlarning to'planishiga olib kelishi mumkin, bu esa kesish sifati va samaradorligiga ta'sir qiladi. Samarali va ekologik toza sovutgichlarni tanlash juda muhimdir. | Pichoq sifati kesishning aniqligi va silliqligiga ta'sir qiladi. Samarasiz sovutish suvi kesish sifati va samaradorligining yomonlashishiga olib kelishi mumkin, bu esa sovutish suvidan optimal foydalanish zarurligini ta'kidlaydi. |
Jarayonni nazorat qilish va sifatni tekshirish | -Jarayonni boshqarish: Kesish jarayonida barqarorlik va izchillikni ta'minlash uchun asosiy kesish parametrlarini real vaqtda kuzatish va sozlash. -Sifatni tekshirish: Kesishdan keyingi tashqi ko'rinishni tekshirish, o'lchov o'lchovlari va elektr ishlashini tekshirish sifat muammolarini tezda aniqlash va hal qilishga yordam beradi, kesish aniqligi va mustahkamligini oshiradi. | Jarayonni to'g'ri nazorat qilish va sifatni tekshirish izchil, yuqori sifatli kesish natijalarini ta'minlashga va yuzaga kelishi mumkin bo'lgan muammolarni erta aniqlashga yordam beradi. |

Kesish sifatini yaxshilash
Kesish sifatini yaxshilash jarayon parametrlarini, uskunalar va materiallarni tanlashni, jarayonni nazorat qilishni va tekshirishni hisobga oladigan kompleks yondashuvni talab qiladi. Kesish texnologiyalarini doimiy ravishda takomillashtirish va jarayon usullarini optimallashtirish orqali gofretni kesishning aniqligi va barqarorligini yanada oshirish mumkin, bu esa yarimo'tkazgich ishlab chiqarish sanoati uchun yanada ishonchli texnik yordam beradi.
#03 Kesishdan keyingi ishlov berish va sinovdan o'tkazish
3.1 Tozalash va quritish
Gofretni kesishdan keyin tozalash va quritish bosqichlari chip sifati va keyingi jarayonlarning silliq rivojlanishini ta'minlash uchun juda muhimdir. Ushbu bosqichda kesish paytida hosil bo'lgan silikon qoldiqlarini, sovutish suvi qoldiqlarini va boshqa ifloslantiruvchi moddalarni yaxshilab olib tashlash kerak. Tozalash jarayonida chiplar shikastlanmasligi va quritgandan so'ng, korroziya yoki elektrostatik oqim kabi muammolarni oldini olish uchun chip yuzasida namlik qolmasligiga ishonch hosil qilish bir xil darajada muhimdir.
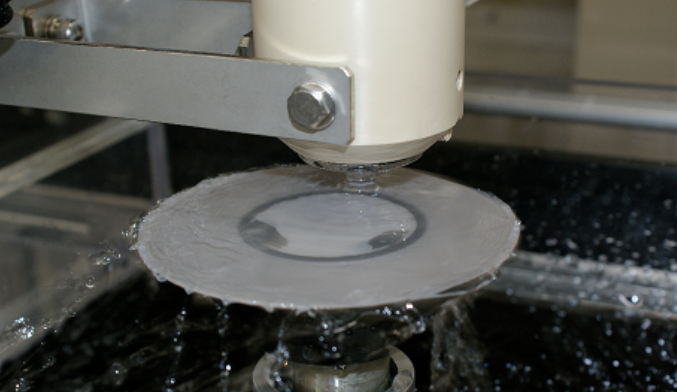
Kesishdan keyingi ishlov berish: tozalash va quritish jarayoni
Jarayon bosqichi | Tarkib | Ta'sir |
Tozalash jarayoni | -Usul: Tozalash uchun ultratovush yoki mexanik cho'tkalash usullari bilan birgalikda maxsus tozalash vositalari va toza suvdan foydalaning. | Ifloslantiruvchi moddalarni to'liq olib tashlashni ta'minlaydi va tozalash vaqtida chiplarning shikastlanishiga yo'l qo'ymaydi. |
-Tozalash vositasini tanlash: Chipga zarar bermasdan samarali tozalashni ta'minlash uchun gofret materiali va ifloslantiruvchi turiga qarab tanlang. | To'g'ri agent tanlash samarali tozalash va chiplarni himoya qilish uchun kalit hisoblanadi. | |
-Parametrlarni boshqarish: Noto'g'ri tozalash natijasida kelib chiqadigan sifat muammolarini oldini olish uchun tozalash harorati, vaqtini va tozalash eritmasi konsentratsiyasini qat'iy nazorat qiling. | Tekshirish moslamalari gofretni shikastlamaslik yoki ifloslantiruvchi moddalarni qoldirmaslikka yordam beradi va barqaror sifatni ta'minlaydi. | |
Quritish jarayoni | -An'anaviy usullar: Past samaradorlikka ega va statik elektr to'planishiga olib kelishi mumkin bo'lgan tabiiy havoni quritish va issiq havo bilan quritish. | Sekinroq quritish vaqtlari va potentsial statik muammolarga olib kelishi mumkin. |
-Zamonaviy texnologiyalar: Chipslar tez quriydi va zararli ta'sirlardan qochish uchun vakuumli quritish va infraqizil quritish kabi ilg'or texnologiyalardan foydalaning. | Tezroq va samaraliroq quritish jarayoni, statik oqim yoki namlik bilan bog'liq muammolar xavfini kamaytiradi. | |
Uskunani tanlash va texnik xizmat ko'rsatish | -Uskunani tanlash: Yuqori samarali tozalash va quritish mashinalari ishlov berish samaradorligini oshiradi va ishlov berish paytida yuzaga kelishi mumkin bo'lgan muammolarni aniq nazorat qiladi. | Yuqori sifatli mashinalar yaxshi ishlov berishni ta'minlaydi va tozalash va quritish paytida xatolar ehtimolini kamaytiradi. |
-Uskunalarga texnik xizmat ko'rsatish: Uskunani muntazam tekshirish va texnik xizmat ko'rsatish uning optimal ish holatida qolishini ta'minlaydi va chip sifatini kafolatlaydi. | To'g'ri parvarishlash uskunalarning ishdan chiqishini oldini oladi, ishonchli va yuqori sifatli ishlov berishni ta'minlaydi. |
Kesishdan keyin tozalash va quritish
Gofretni kesishdan keyin tozalash va quritish bosqichlari murakkab va nozik jarayonlar bo'lib, yakuniy ishlov berish natijasini ta'minlash uchun bir nechta omillarni diqqat bilan ko'rib chiqishni talab qiladi. Ilmiy usullar va qat'iy protseduralardan foydalangan holda, har bir chipning keyingi qadoqlash va sinov bosqichlariga optimal holatda kirishini ta'minlash mumkin.
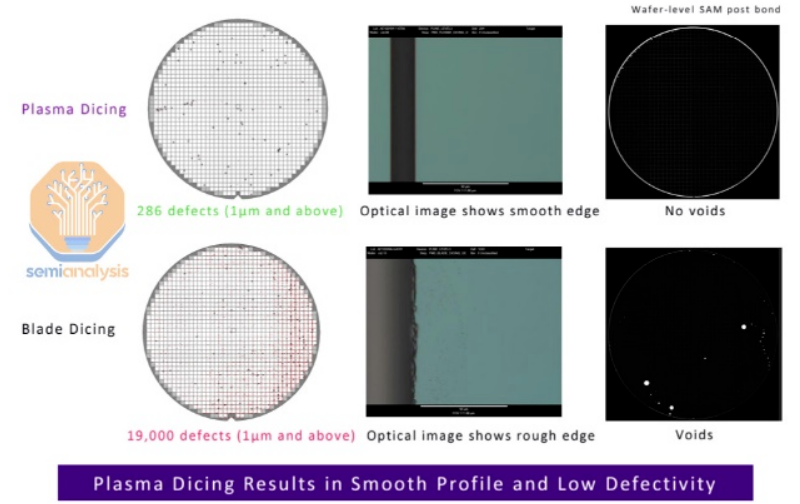
Kesishdan keyingi tekshirish va sinov
Qadam | Tarkib | Ta'sir |
Tekshirish bosqichi | 1.Vizual tekshirish: Yoriqlar, chiplar yoki chip yuzasida ifloslanish kabi ko'rinadigan nuqsonlarni tekshirish uchun vizual yoki avtomatlashtirilgan tekshirish uskunasidan foydalaning. Chiqindilarga yo'l qo'ymaslik uchun jismoniy shikastlangan chiplarni tezda aniqlang. | Jarayonning boshida nuqsonli chiplarni aniqlash va yo'q qilish, moddiy yo'qotishlarni kamaytirishga yordam beradi. |
2.Hajmi o'lchovi: Chip o'lchamlarini aniq o'lchash, kesilgan o'lchamning dizayn xususiyatlariga mos kelishini ta'minlash va ishlash muammolari yoki qadoqlash qiyinchiliklarini oldini olish uchun nozik o'lchash moslamalaridan foydalaning. | Chiplarning talab qilinadigan o'lcham chegaralarida bo'lishini ta'minlaydi, ishlashning pasayishi yoki montaj muammolarini oldini oladi. | |
3.Elektr ishlashi testi: Mos kelmaydigan mikrosxemalar aniqlash va keyingi bosqichga faqat ishlashga mos chiplar o'tishini ta'minlash uchun qarshilik, sig'im va indüktans kabi asosiy elektr parametrlarini baholang. | Jarayonda faqat funktsional va ishlash sinovidan o'tgan chiplarning oldinga siljishini ta'minlaydi va keyingi bosqichlarda ishdan chiqish xavfini kamaytiradi. | |
Sinov bosqichi | 1.Funktsional test: Chipning asosiy funksionalligi maqsadga muvofiq ishlayotganligini tekshiring, funktsional anormalliklari bo'lgan chiplarni aniqlang va yo'q qiling. | Keyingi bosqichlarga o'tishdan oldin chiplarning asosiy operatsion talablarga javob berishini ta'minlaydi. |
2.Ishonchlilik testi: Uzoq muddatli foydalanish yoki og'ir muhitda chipning ishlashi barqarorligini baholang, bu odatda yuqori haroratli qarish, past harorat sinovlari va haqiqiy ekstremal sharoitlarni taqlid qilish uchun namlik sinovlarini o'z ichiga oladi. | Chipslarning turli xil ekologik sharoitlarda ishonchli ishlashini ta'minlaydi, mahsulotning uzoq umr va barqarorligini oshiradi. | |
3.Muvofiqlik testi: Chipning boshqa komponentlar yoki tizimlar bilan to'g'ri ishlashini tekshiring, hech qanday nosozlik yoki nomuvofiqlik tufayli ishlashning pasayishiga ishonch hosil qiling. | Muvofiqlik bilan bog'liq muammolarni oldini olish orqali haqiqiy ilovalarda uzluksiz ishlashni ta'minlaydi. |
3.3 Qadoqlash va saqlash
Gofret kesilgandan so'ng, chiplar yarimo'tkazgich ishlab chiqarish jarayonining muhim mahsulotidir va ularni qadoqlash va saqlash bosqichlari bir xil darajada muhimdir. To'g'ri qadoqlash va saqlash choralari nafaqat tashish va saqlash paytida chiplarning xavfsizligi va barqarorligini ta'minlash, balki keyingi ishlab chiqarish, sinov va qadoqlash bosqichlarini kuchli qo'llab-quvvatlash uchun ham muhimdir.
Tekshirish va sinov bosqichlarining qisqacha mazmuni:
Gofretni kesishdan keyin chiplarni tekshirish va sinovdan o'tkazish bosqichlari vizual tekshirish, o'lchamni o'lchash, elektr ishlashi testi, funktsional test, ishonchlilik sinovi va muvofiqlik sinovi kabi bir qator jihatlarni qamrab oladi. Ushbu bosqichlar bir-biriga bog'langan va bir-birini to'ldiruvchi bo'lib, mahsulot sifati va ishonchliligini ta'minlash uchun mustahkam to'siqni tashkil qiladi. Qattiq tekshirish va sinov tartib-qoidalari orqali potentsial muammolarni tezda aniqlash va hal qilish mumkin, bu yakuniy mahsulot mijozning talablari va kutishlariga javob beradi.
Aspekt | Tarkib |
Qadoqlash choralari | 1.Antistatik: Qadoqlash materiallari statik elektrning qurilmalarga zarar etkazishi yoki ularning ishlashiga ta'sir qilmasligi uchun mukammal antistatik xususiyatlarga ega bo'lishi kerak. |
2.Namlikka chidamli: O'rash materiallari korroziya va namlik tufayli elektr quvvatining yomonlashishini oldini olish uchun yaxshi namlikka chidamli bo'lishi kerak. | |
3.Shokka chidamli: Qadoqlash materiallari chiplarni tashish paytida tebranish va ta'sirdan himoya qilish uchun samarali zarba yutilishini ta'minlashi kerak. | |
Saqlash muhiti | 1.Namlikni nazorat qilish: Haddan tashqari namlik yoki past namlikdan kelib chiqadigan statik muammolar tufayli namlikni yutish va korroziyani oldini olish uchun namlikni tegishli diapazonda qat'iy nazorat qiling. |
2.Tozalik: Chiplarni chang va aralashmalar bilan ifloslantirmaslik uchun toza saqlash muhitini saqlang. | |
3.Haroratni nazorat qilish: Haddan tashqari issiqlik yoki past haroratlardan kelib chiqadigan kondensatsiya muammolari tufayli tez qarishni oldini olish uchun mos harorat oralig'ini o'rnating va harorat barqarorligini saqlang. | |
Doimiy tekshirish | Potensial muammolarni o'z vaqtida aniqlash va hal qilish uchun vizual tekshiruvlar, o'lcham o'lchovlari va elektr ishlashi testlaridan foydalangan holda saqlangan chiplarni muntazam ravishda tekshiring va baholang. Saqlash vaqti va shartlariga asoslanib, ularning optimal holatda ishlatilishini ta'minlash uchun chiplardan foydalanishni rejalashtiring. |
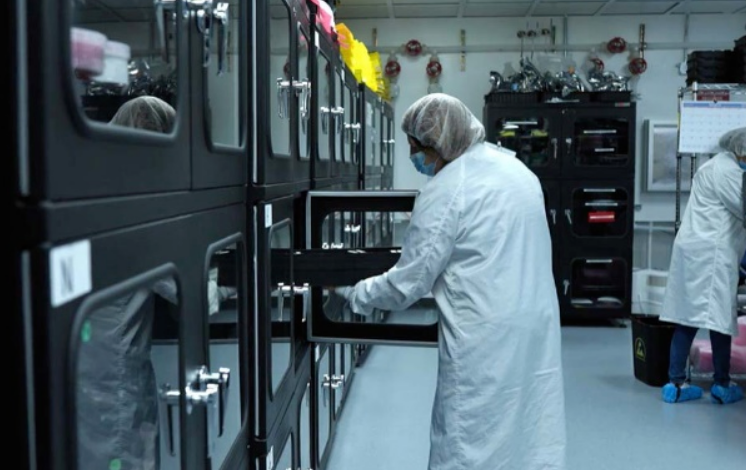
Gofretni kesish jarayonida mikro yoriqlar va shikastlanishlar muammosi yarimo'tkazgichlarni ishlab chiqarishda muhim muammo hisoblanadi. Kesish stressi bu hodisaning asosiy sababidir, chunki u gofret yuzasida mayda yoriqlar va shikastlanishlar hosil qiladi, bu esa ishlab chiqarish xarajatlarining oshishiga va mahsulot sifatining pasayishiga olib keladi.
Ushbu muammoni hal qilish uchun kesish stressini minimallashtirish va optimallashtirilgan kesish texnikasi, asboblari va shartlarini amalga oshirish juda muhimdir. Pichoq materiali, kesish tezligi, bosim va sovutish usullari kabi omillarga ehtiyotkorlik bilan e'tibor berish mikro yoriqlar shakllanishini kamaytirishga va jarayonning umumiy hosildorligini oshirishga yordam beradi. Bundan tashqari, lazerli kesish kabi ilg'or kesish texnologiyalari bo'yicha olib borilayotgan tadqiqotlar ushbu muammolarni yanada yumshatish yo'llarini o'rganmoqda.
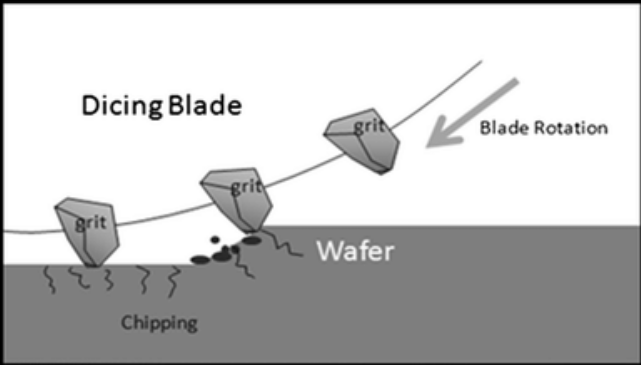
Mo'rt material sifatida gofretlar mexanik, termal yoki kimyoviy stressga duchor bo'lganda ichki strukturaviy o'zgarishlarga moyil bo'lib, mikro yoriqlar paydo bo'lishiga olib keladi. Garchi bu yoriqlar darhol sezilmasa ham, ular kengayib, ishlab chiqarish jarayonining rivojlanishi bilan yanada jiddiy zarar etkazishi mumkin. Bu muammo, ayniqsa, keyingi qadoqlash va sinov bosqichlarida muammoli bo'lib qoladi, bunda haroratning o'zgarishi va qo'shimcha mexanik stresslar bu mikro yoriqlar ko'rinadigan yoriqlarga aylanishi mumkin, bu esa chiplarning ishdan chiqishiga olib keladi.
Ushbu xavfni kamaytirish uchun kesish tezligi, bosim va harorat kabi parametrlarni optimallashtirish orqali kesish jarayonini diqqat bilan nazorat qilish kerak. Lazerli kesish kabi kamroq agressiv kesish usullaridan foydalanish gofretdagi mexanik kuchlanishni kamaytirishi va mikro yoriqlar hosil bo'lishini minimallashtirishi mumkin. Bundan tashqari, gofretni kesish jarayonida infraqizil skanerlash yoki rentgen nurlari kabi ilg'or tekshirish usullarini qo'llash ushbu dastlabki bosqichdagi yoriqlarni keyingi shikastlanishga olib kelishidan oldin aniqlashga yordam beradi.
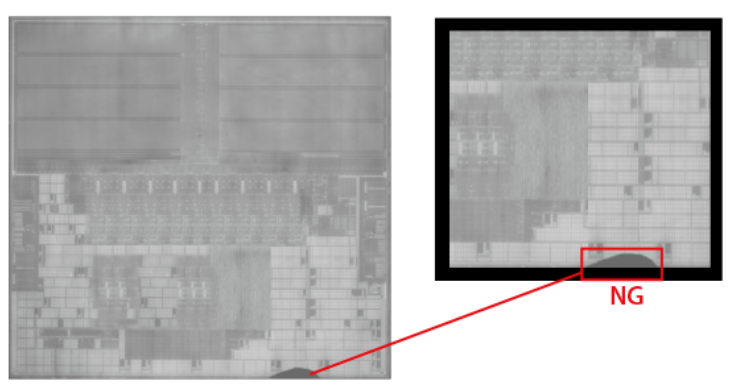
Gofret yuzasining shikastlanishi zarni kesish jarayonida jiddiy tashvish tug'diradi, chunki u chipning ishlashi va ishonchliligiga bevosita ta'sir qilishi mumkin. Bunday zararni kesish asboblarini noto'g'ri ishlatish, noto'g'ri kesish parametrlari yoki gofretning o'ziga xos bo'lgan moddiy nuqsonlari sabab bo'lishi mumkin. Sababi nima bo'lishidan qat'i nazar, bu shikastlanishlar elektr qarshiligi yoki kontaktlarning zanglashiga olib keladigan sig'imidagi o'zgarishlarga olib kelishi mumkin, bu umumiy ishlashga ta'sir qiladi.
Ushbu muammolarni hal qilish uchun ikkita asosiy strategiya o'rganilmoqda:
1.Kesish asboblari va parametrlarini optimallashtirish: O'tkirroq pichoqlardan foydalanish, kesish tezligini sozlash va kesish chuqurligini o'zgartirish orqali kesish jarayonida stress kontsentratsiyasini minimallashtirish mumkin, bu esa shikastlanish ehtimolini kamaytiradi.
2. Yangi kesish texnologiyalarini o'rganish: Lazerli kesish va plazma bilan kesish kabi ilg'or texnikalar yaxshilangan aniqlikni ta'minlaydi va gofretga etkazilgan zarar darajasini pasaytiradi. Ushbu texnologiyalar gofretdagi termal va mexanik kuchlanishni minimallashtirishda yuqori kesish aniqligiga erishish yo'llarini topish uchun o'rganilmoqda.
Issiqlik ta'sir doirasi va uning ishlashga ta'siri
Lazer va plazma bilan kesish kabi termal kesish jarayonlarida yuqori harorat muqarrar ravishda gofret yuzasida termal ta'sir zonasini yaratadi. Harorat gradienti muhim bo'lgan bu maydon materialning xususiyatlarini o'zgartirishi mumkin, bu chipning yakuniy ishlashiga ta'sir qiladi.
Termal ta'sir zonasining (TAZ) ta'siri:
Kristal tuzilmasining o'zgarishi: Yuqori haroratlarda gofret materialidagi atomlar qayta joylashishi mumkin, bu esa kristall strukturasida buzilishlarga olib keladi. Bu buzilish materialni zaiflashtiradi, uning mexanik mustahkamligi va barqarorligini pasaytiradi, bu esa foydalanish paytida chiplarning ishdan chiqishi xavfini oshiradi.
Elektr xususiyatlarining o'zgarishi: Yuqori haroratlar yarimo'tkazgich materiallarida tashuvchining kontsentratsiyasini va harakatchanligini o'zgartirishi mumkin, bu chipning elektr o'tkazuvchanligiga va oqim uzatish samaradorligiga ta'sir qiladi. Ushbu o'zgarishlar chipning ishlashining pasayishiga olib kelishi mumkin, bu esa uni mo'ljallangan maqsadiga yaroqsiz holga keltirishi mumkin.
Ushbu ta'sirlarni yumshatish uchun kesish paytida haroratni nazorat qilish, kesish parametrlarini optimallashtirish va sovutish oqimlari yoki ishlov berishdan keyingi ishlov berish kabi usullarni o'rganish termal ta'sir darajasini kamaytirish va materialning yaxlitligini saqlash uchun muhim strategiyalardir.
Umuman olganda, mikro yoriqlar va termal ta'sir zonalari gofretni kesish texnologiyasida hal qiluvchi muammolardir. Yarimo'tkazgich mahsulotlarining sifatini yaxshilash va ularning bozor raqobatbardoshligini oshirish uchun texnologik yutuqlar va sifat nazorati choralari bilan bir qatorda davomli tadqiqotlar zarur bo'ladi.
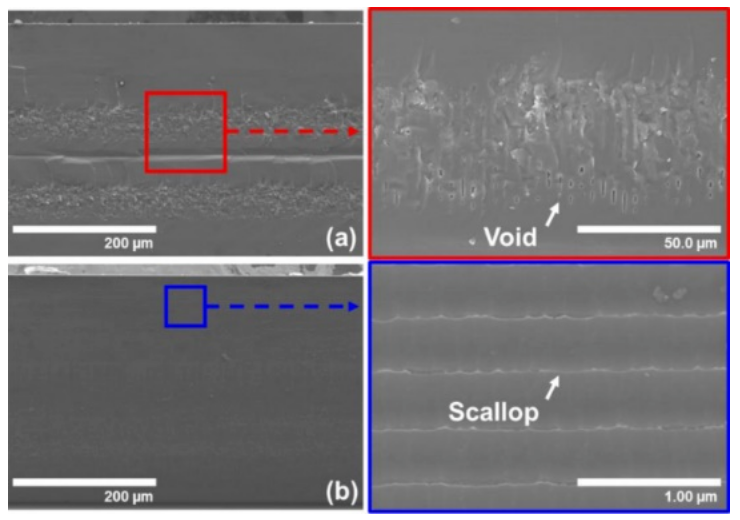
Termal ta'sir zonasini nazorat qilish choralari:
Kesish jarayoni parametrlarini optimallashtirish: Kesish tezligi va quvvatini kamaytirish termal ta'sir zonasi (TAZ) hajmini samarali ravishda kamaytirishi mumkin. Bu kesish jarayonida hosil bo'ladigan issiqlik miqdorini nazorat qilishda yordam beradi, bu gofretning moddiy xususiyatlariga bevosita ta'sir qiladi.
Ilg'or sovutish texnologiyalari: Suyuq azotli sovutish va mikrosuyuqlik bilan sovutish kabi texnologiyalarni qo'llash termal ta'sir zonasi diapazonini sezilarli darajada cheklashi mumkin. Ushbu sovutish usullari issiqlikni samaraliroq tarqatishga yordam beradi, shu bilan gofretning material xususiyatlarini saqlab qoladi va termal zararni minimallashtiradi.
Materialni tanlash: Tadqiqotchilar mukammal issiqlik o'tkazuvchanligi va mexanik kuchga ega bo'lgan uglerod nanotubalari va grafen kabi yangi materiallarni o'rganishmoqda. Ushbu materiallar chiplarning umumiy ish faoliyatini yaxshilash bilan birga termal ta'sir zonasini kamaytirishi mumkin.
Xulosa qilib aytganda, termal ta'sir zonasi termal kesish texnologiyalarining muqarrar natijasi bo'lsa-da, uni optimallashtirilgan ishlov berish texnikasi va material tanlash orqali samarali boshqarish mumkin. Kelajakdagi tadqiqotlar gofretni yanada samarali va aniq kesishga erishish uchun termal kesish jarayonlarini nozik sozlash va avtomatlashtirishga qaratiladi.

Balans strategiyasi:
Gofret hosildorligi va ishlab chiqarish samaradorligi o'rtasidagi optimal muvozanatga erishish gofretni kesish texnologiyasida doimiy muammo hisoblanadi. Ishlab chiqaruvchilar oqilona ishlab chiqarish strategiyasi va jarayon parametrlarini ishlab chiqish uchun bozor talabi, ishlab chiqarish xarajatlari va mahsulot sifati kabi bir nechta omillarni hisobga olishlari kerak. Shu bilan birga, ilg'or kesish uskunalarini joriy etish, operatorlar malakasini oshirish va xom ashyo sifatini nazorat qilishni kuchaytirish ishlab chiqarish samaradorligini oshirish bilan birga hosilni saqlash yoki hatto yaxshilash uchun muhimdir.
Kelajakdagi muammolar va imkoniyatlar:
Yarimo'tkazgich texnologiyasining rivojlanishi bilan gofretni kesish yangi muammolar va imkoniyatlarga duch keladi. Chip o'lchamlari kichrayib, integratsiya oshgani sayin, kesishning aniqligi va sifatiga bo'lgan talablar sezilarli darajada oshadi. Shu bilan birga, rivojlanayotgan texnologiyalar gofretni kesish texnikasini rivojlantirish uchun yangi g'oyalarni taqdim etadi. Ishlab chiqaruvchilar bozor dinamikasi va texnologik tendentsiyalarga mos kelishi, bozor o'zgarishlari va texnologik talablarni qondirish uchun ishlab chiqarish strategiyalari va jarayon parametrlarini doimiy ravishda moslashtirishi va optimallashtirishi kerak.
Xulosa qilib aytganda, bozor talabi, ishlab chiqarish xarajatlari va mahsulot sifatini hisobga olgan holda, ilg'or asbob-uskunalar va texnologiyalarni joriy etish, operator malakasini oshirish va xom ashyo nazoratini kuchaytirish orqali ishlab chiqaruvchilar gofretni kesish jarayonida gofret hosildorligi va ishlab chiqarish samaradorligi o'rtasidagi eng yaxshi muvozanatga erishishlari mumkin, bu esa samarali va yuqori sifatli yarimo'tkazgichli mahsulot ishlab chiqarishga olib keladi.
Kelajakdagi istiqbol:
Tez texnologik taraqqiyot bilan yarimo'tkazgich texnologiyasi misli ko'rilmagan sur'atlarda rivojlanmoqda. Yarimo'tkazgichlarni ishlab chiqarishda muhim qadam sifatida gofretni kesish texnologiyasi hayajonli yangi ishlanmalarga tayyor. Oldinga qarab, gofretni kesish texnologiyasi aniqlik, samaradorlik va xarajat bo'yicha sezilarli yaxshilanishlarga erishib, yarimo'tkazgich sanoatining doimiy o'sishiga yangi hayotiylik kiritishi kutilmoqda.
Aniqlikni oshirish:
Yuqori aniqlikka intilishda gofretni kesish texnologiyasi doimiy ravishda mavjud jarayonlarning chegaralarini kengaytiradi. Kesish jarayonining fizik va kimyoviy mexanizmlarini chuqur o'rganish va kesish parametrlarini aniq nazorat qilish orqali, borgan sari murakkab sxemani loyihalash talablariga javob beradigan nozik kesish natijalariga erishiladi. Bundan tashqari, yangi materiallar va kesish usullarini o'rganish hosil va sifatni sezilarli darajada yaxshilaydi.
Samaradorlikni oshirish:
Yangi gofret kesish uskunasi aqlli va avtomatlashtirilgan dizaynga e'tibor qaratadi. Ilg'or boshqaruv tizimlari va algoritmlarini joriy etish asbob-uskunalarni turli materiallar va dizayn talablarini qondirish uchun kesish parametrlarini avtomatik ravishda sozlash imkonini beradi va shu bilan ishlab chiqarish samaradorligini sezilarli darajada oshiradi. Ko'p gofretli kesish texnologiyasi va pichoqni tez almashtirish tizimlari kabi innovatsiyalar samaradorlikni oshirishda hal qiluvchi rol o'ynaydi.
Xarajatlarni kamaytirish:
Xarajatlarni kamaytirish gofretni kesish texnologiyasini rivojlantirishning asosiy yo'nalishi hisoblanadi. Yangi materiallar va kesish usullari ishlab chiqilganligi sababli, uskunalar xarajatlari va texnik xizmat ko'rsatish xarajatlari samarali nazorat qilinishi kutilmoqda. Bundan tashqari, ishlab chiqarish jarayonlarini optimallashtirish va chiqindilarni kamaytirish ishlab chiqarish jarayonida chiqindilarni yanada kamaytiradi, bu esa umumiy ishlab chiqarish xarajatlarining pasayishiga olib keladi.
Aqlli ishlab chiqarish va IoT:
Aqlli ishlab chiqarish va narsalar Interneti (IoT) texnologiyalarining integratsiyasi gofret kesish texnologiyasiga transformativ o'zgarishlar olib keladi. O'zaro bog'liqlik va qurilmalar o'rtasida ma'lumot almashish orqali ishlab chiqarish jarayonining har bir bosqichi real vaqt rejimida kuzatilishi va optimallashtirilishi mumkin. Bu nafaqat ishlab chiqarish samaradorligi va mahsulot sifatini oshiradi, balki kompaniyalarga bozorni aniqroq bashorat qilish va qaror qabul qilishda yordam beradi.
Kelajakda gofretni kesish texnologiyasi aniqlik, samaradorlik va narx bo'yicha ajoyib yutuqlarga erishadi. Ushbu yutuqlar yarimo'tkazgich sanoatining uzluksiz rivojlanishiga turtki bo'ladi va insoniyat jamiyatiga ko'proq texnologik innovatsiyalar va qulayliklar olib keladi.
Yuborilgan vaqt: 2024 yil 19-noyabr